Select a language:
Roux, a proactive, outgoing, perfectionist with strong analytical skills, was hired to carry out a complex tappet placement project on a truck’s engine block. The task was to place a tappet in eight to sixteen holes without damaging either the tappets or the engine bores, all within a tight deadline. However, early on, he realized that there were delays in the delivery of electrical and mechanical components, which compromised the progress of the project.
Faced with this situation, Roux did not hesitate to step in and reorganize all aspects of the project to ensure its success. He knew he had to readjust the initial goals and objectives to align them with those of the organization and, at the same time, ensure that the project moved forward smoothly. To do this, he identified the need for an experienced PLC programmer and robot programmer to successfully integrate and complete a large abandoned program, a complex challenge that would require completely new logic.
Using his extensive network of contacts at Leadec, Roux contacted a RELANT Automation field engineer who possessed the perfect combination of standards programming experience, intuitive acumen and a firm commitment to excellence.
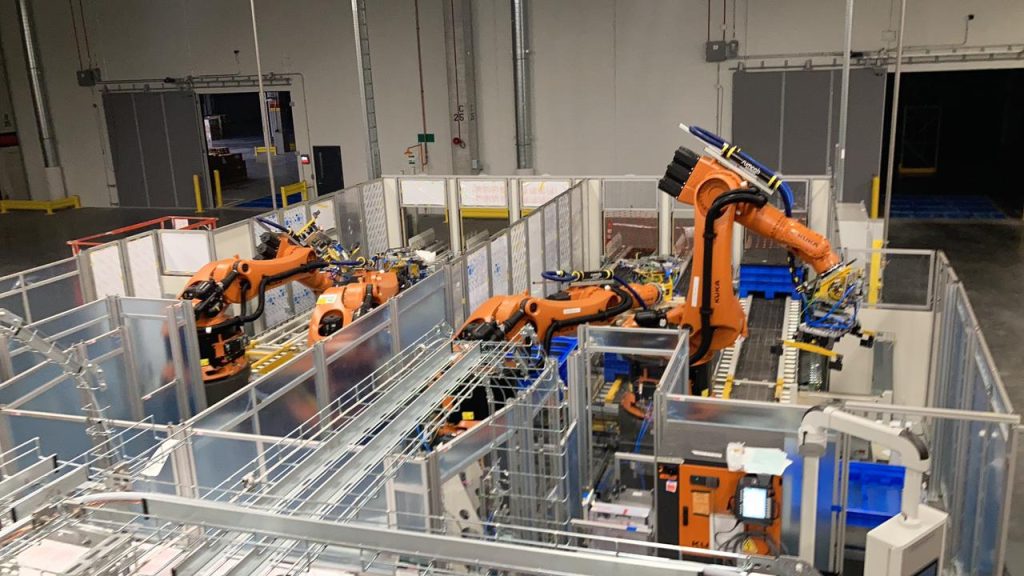
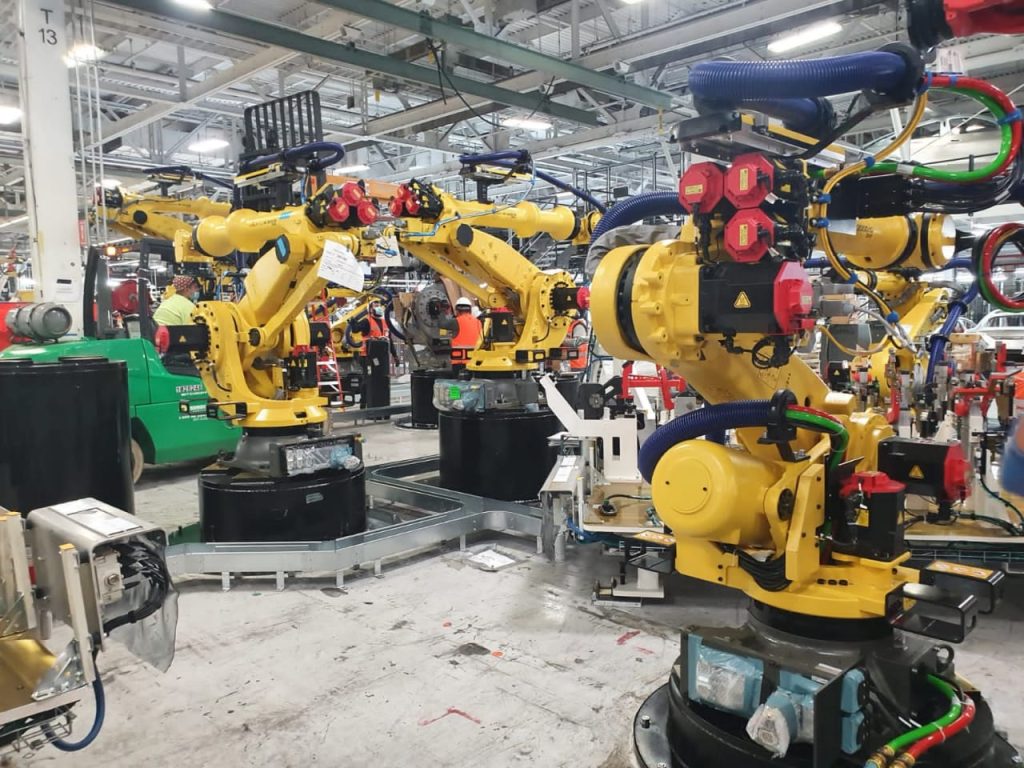
Together they began to discuss the objectives and constraints of the project, and it was then that the PLC programmer suggested a number of approaches for integration, based on breaking down the programming structure into more manageable sections. In this way, each could be achieved, tested and reported to the customer in a timely manner.
The main sections of the project included:
- Conveyor logic: To feed the parts in the correct position and with the correct orientation, using the SEW Movimot motor.
- Gripper logic: For gripping the parts and placing them in the motor bores, with the IAI application.
- Robot Interfaces: Implementing the handshakes between the PLC and the robot, both in manual and automatic mode.
- Manual function interlocks: Developed through PLC and HMI under the Transline standard.
- Automatic sequence interlocking: Managed by RFID through PLC and HMI.
- Manual/automatic interconnection with an existing line: Using a PNP coupler.
- Diagnostics: Implementation of fault messaging to ensure correct system operation.
Tappet placement process:
The PLC program was designed to precisely control each service by torque, working in conjunction with the IAI controller. The robot was set to follow a strict path to avoid damage to both the engine and tappets. In addition, an oil application function was developed, which consisted of spreading oil into the tappet bores, ensuring proper lubrication.
To prevent collisions, a manual interlocking function was included between the conveyor movement and the robot, ensuring that the two systems did not interfere with each other. Each process was recorded in detail in the RFID system, allowing accurate tracking of progress.
Once the robot released the supports and moved to the next station, the HMI (Human Machine Interface) took over control of diagnostics and fault messaging. In addition, a Transline structure was developed, which facilitated visualization and control of the sequence of operations, with clear diagnostic rules and manual/automatic modes.
To ensure that the entire system worked properly, a dry cycle test was run to verify the insertion of parts according to the newly developed concept.
In the end, thanks to Roux’s dedication and organizational skills, the project manager was able to transform a manual station into a fully automated one, meeting all of the client’s objectives. After the demonstration of the automated process, the client was pleased to see how smoothly the entire system operated, and the project was completed within the allocated budget.