Select a language:
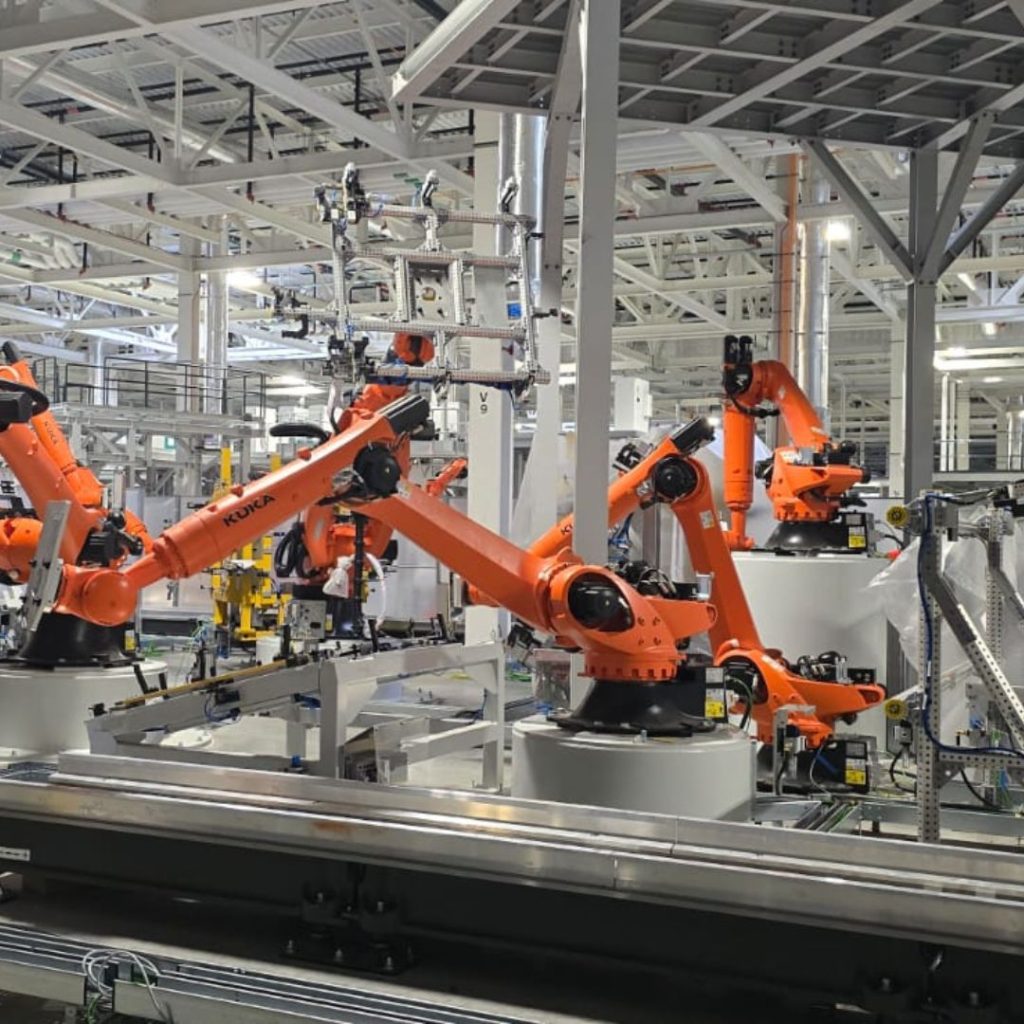
In 2017, King Automation’s programming leader took on a crucial project for Mercedes Benz. This was a dedicated, friendly, hard-working man, a natural team leader and an expert network builder. He had a clear vision and was determined to make it a reality.
The challenge was monumental: in just three months, he had to ensure that the project moved forward in the plant’s body shop on a tight schedule, almost like clockwork.
To achieve this, he would need more than just his technical expertise; it would require all his ability to manage people and resources, and, above all, his extensive network of trusted professionals. Among them, he had previously collaborated with several, some of whom he had met during past projects.
One of those key contacts was Eduardo, a Relant Automation engineer whom I had met the previous year during a major project in Mexico. Eduardo had valuable experience in installing body shops and was an expert at quickly familiarizing new programmers with Siemens standards, a crucial aspect of the project’s success.
Quickly, Strobel, the leader of King Automation, recruited Eduardo, pulling him from a smaller project to join the team. At their first meeting, Strobel explained the magnitude of the challenge:
“We will have to develop a standard program and train new employees to apply it across all lines. Consistency will be key; each line must meet the customer’s requirements perfectly,” Strobel explained to Eduardo. “We will roll out each line one at a time and set detailed weekly deadlines to keep pace. This is a team effort and we will all share in the achievement. We will start strong and meet this demanding deadline.”
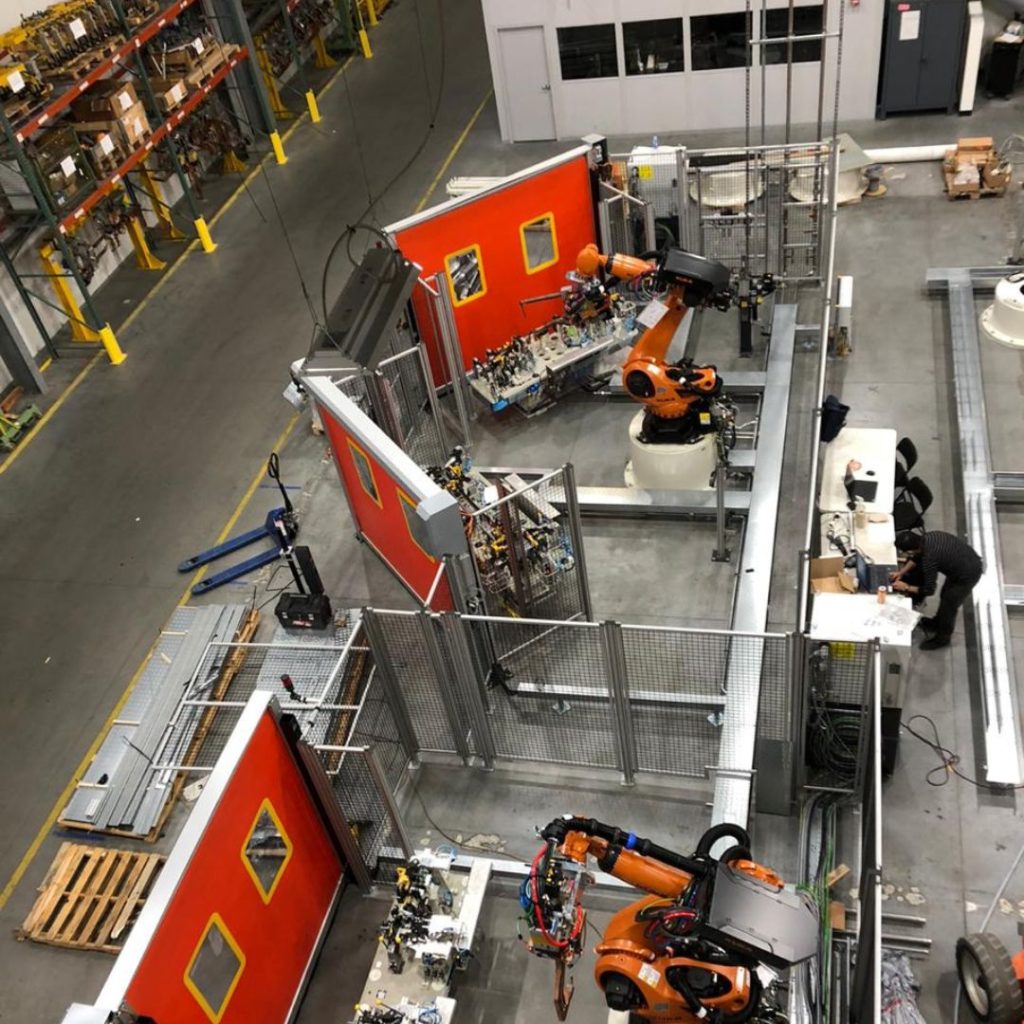
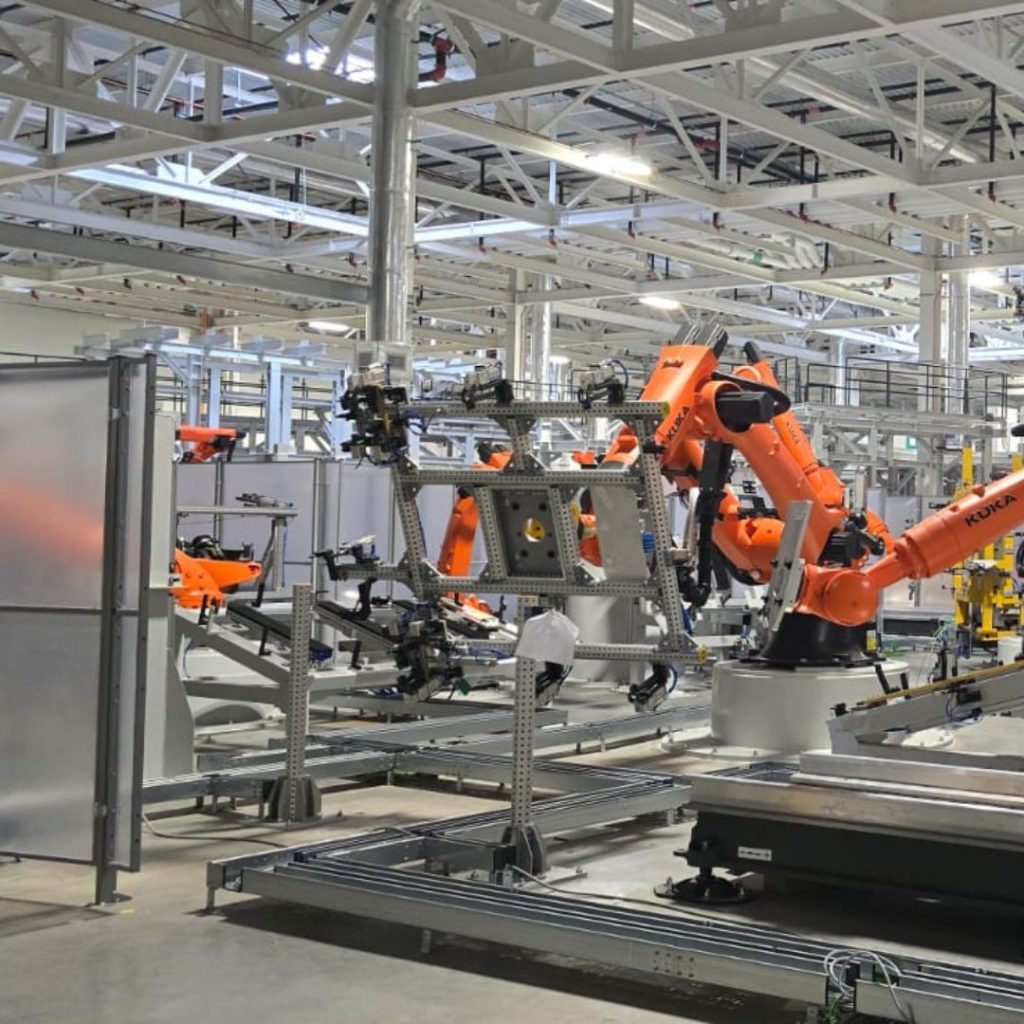
The Relant Automation team, with Strobel’s collaboration, implemented Integra Wave 5 to facilitate the development of the project. This allowing them to efficiently and accurately manage critical tasks such as:
- The integrated design, wiring diagrams and panel layout for eight lines ensured that they could be properly managed, verified and delivered.
- On-site electrical installation.
- The development of new offline PLC programs.
- The creation of program simulation and debugging processes.
- Setting up and adjusting new trajectories for robot programs.
- The configuration and commissioning of servo drives.
In addition, Relant Automation was responsible for the creation of the first wiring diagrams, the device list, the symbol table and the start of the program standard. Its programmers took on the task of verifying the network configuration to ensure that the interface between devices was fully operational.
The team was also responsible for ongoing tasks essential to the success of the project, such as:
- IO checks together with the electrician.
- Manual debugging, verifying the interlocking between process functions.
- Configuration, debugging and implementation of the security program to meet certification standards.
The work of configuring, debugging and commissioning the automatic functions was critical, and as with any project of this magnitude, dry-cycling was performed constantly, fine-tuning the teamwork to ensure that, once production started, all functions would run smoothly and quickly.
Eduardo and his team at Relant Automation not only met the deadlines, but made the 2017 Mercedes Benz V167 project a true success. For Eduardo, this project became one of the highlights of his engineering career, an accomplishment he would always remember with pride.