Select a language:
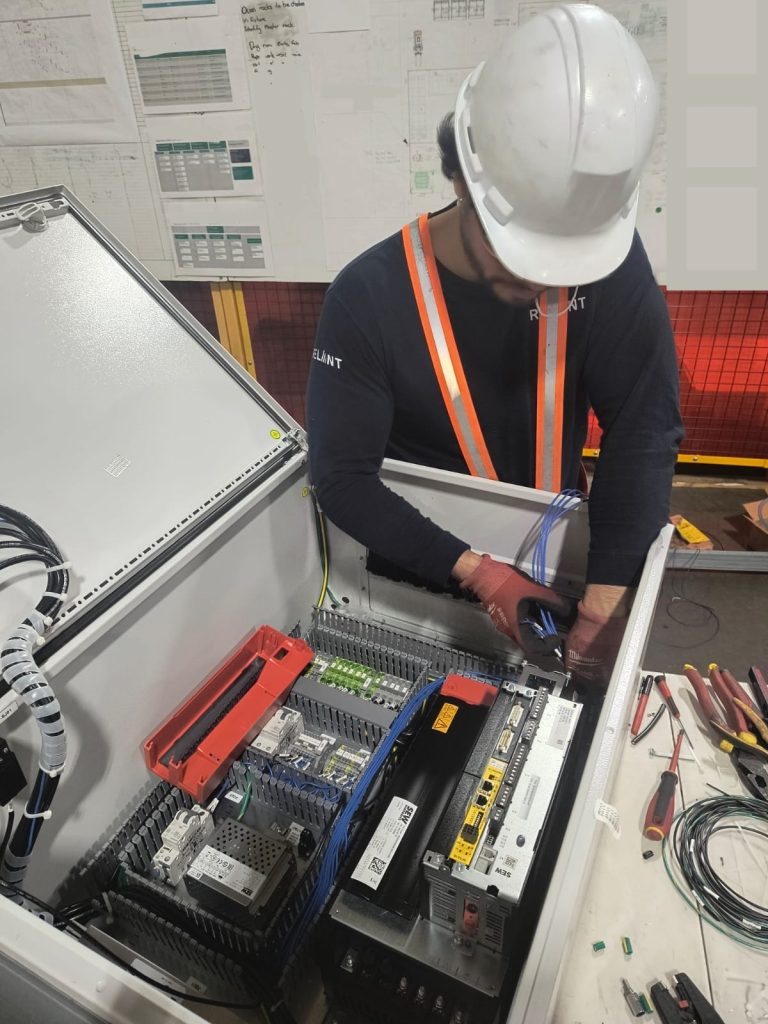
A Case Study in Toluca, Mexico
Comau, a renowned Italian company specialized in industrial automation, was selected to carry out a key project for FCA to integrate the new MP model into its existing production lines. Comau’s experience as a systems integrator, together with its focus on improving manufacturing and automation processes, made it the ideal choice for this challenge.
Project Details:
The project involved a series of complex modifications to standard and safety programs in several areas of the plant, including:
- Rear floor
- First floor
- Bass lines
- Body side
- Top pallet manager
- Framer Line
Project Summary:
- Creation of a new logic application to integrate 72 new robots into the existing network. The robots involved were of NACHI, ABB and COMAU brands, and included:
- Material handling robots.
- Welding robots.
- Robots for gluing and sealing guns.
- Commissioning and integration of multiple Emerson Unidrive applications.
- Elimination of NACHI robots and integration of COMAU robots into existing lines.
- Significantly improved cycle time to optimize efficiency.
- Development of the logic to incorporate new variants and adapt to future changes.
- Creation of new interfaces to ensure effective communication with the new robots.
- Training of maintenance personnel to ensure the correct operation of the new integration lines and to provide long-term technical support.
The project control manager excelled at delegating tasks and building effective teams. His first challenge was to assemble a team of engineers with automotive experience, experts in making the most of the open information protocol of the Comau Legacy standard.
To increase the stability and safety of the system, a PILZ PS3000 controller was integrated to monitor the NACHI robots, while the new COMAU robots were integrated into each line. In addition, a function block was developed and modified, ensuring that each of the six lines had at least three PILZ processors to ensure efficient control.
Team Actions:
- Elimination of the existing application to allow the integration of new technologies.
- Creation and launch of the new application based on the specific needs of the project.
- Modification of the existing application to implement a security device, which included:
- Safety switches.
- Emergency stops.
- Dead man’s devices.
- Photoelectric curtains per zone.
- Laser scanners.
- Delimited work areas.
- Interlocking of safety PLC zones, with muting functions.
- Doors with security lock.
Standard PLC programs were developed using Studio 5000, and multiple meetings were held between the development team and the PLC programmer to ensure that the safety application covered all six lines of the Body Shop.
Improvements and Optimization:
The Control Director was committed to continuous improvement and to the effective integration of all activities through the use of Process Analysis software. In addition, work was done on improving existing logic and incorporating new concepts, ensuring that the entire system was optimized to guarantee optimum safety.
Key steps for improvement included:
- Understanding of the reading logic of the application of functions.
- Integration of the new logic without discarding the useful elements of the existing logic.
- Logic debugging and extensive testing to ensure proper implementation.
- Development of functional application logic for the new COMAU robots, using PILZ PS3000.
Integration of new safety devices (safety switches, light curtains, safety doors, laser scanners) in accordance with the standard.
Collaboration and Project Success:
Relant Automation was excited to have the opportunity to bring a fresh and valuable perspective to Comau’s project. Working closely together, the Relant team and Comau executed each task with care, demonstrating steady, step-by-step progress.
The strong sense of commitment and teamwork was crucial to ensure the success of the project, even in the face of the most complex challenges. Thanks to this effective collaboration, the project was successfully completed, improving plant efficiency and optimizing the integration of new technologies with existing lines.